The Vital Role of a Mold Manufacturer in Modern Manufacturing
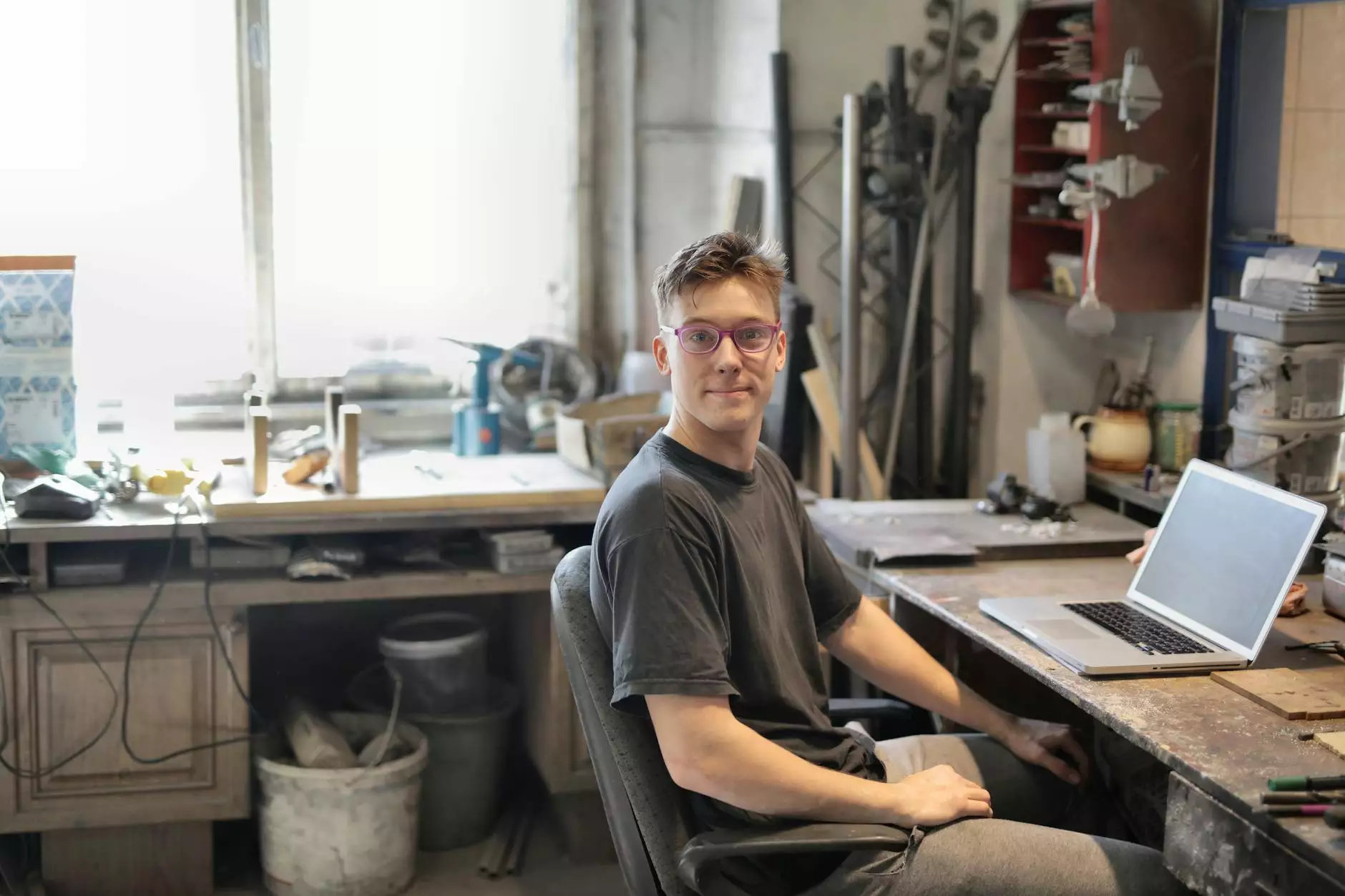
In today's rapidly evolving industrial landscape, mold manufacturers stand as the backbone of the manufacturing process. Their importance cannot be overstated, particularly in sectors that demand precision and durability, such as in metal fabrication. At DeepMould.net, we excel in providing innovative molding solutions that enhance production efficiency and product quality.
Understanding Mold Manufacturing
Mold manufacturing involves a sophisticated process dedicated to creating tools that shape materials (most commonly metals and plastics) into specific forms. This includes both the initial design and fabrication of the molds, as well as the assembly and maintenance of these pivotal production tools.
What Does a Mold Manufacturer Do?
The work of a mold manufacturer includes several critical steps:
- Conceptual Design: Creating designs based on client specifications, industry standards, and material properties.
- Prototyping: Producing prototypes to validate design functionality before full-scale production.
- Fabrication: Manufacturing the molds using advanced machining techniques and technology to ensure precision.
- Quality Control: Implementing stringent quality assurance processes to guarantee the molds meet required specifications and tolerances.
- Maintenance and Upgrades: Providing ongoing maintenance for molds to extend their life cycle and adapt to new production requirements.
The Importance of Precision in Mold Manufacturing
Precision is a crucial element in the role of any mold manufacturer. In the realm of metal fabricators, where tolerances can be minimal, the accuracy of molds directly impacts the quality of the final product. Ensuring that molds are created with utmost precision reduces waste and enhances productivity.
Key Benefits of Precision Molding
The significance of precision in molding cannot be overstated. Here are some benefits:
- Enhanced Product Quality: Accurate molds lead to consistently high-quality products.
- Reduced Manufacturing Costs: Minimizing errors through precision cuts down on material waste and rework expenses.
- Faster Production Times: Precise molds streamline the production process, enabling quicker turnaround times.
- Better Customer Satisfaction: Customers receive reliable and high-quality products that meet or exceed their expectations.
Material Considerations in Mold Manufacturing
Choosing the right materials for molds is another critical aspect of the manufacturing process. DeepMould.net utilizes a variety of materials including:
- Tool Steel: Known for its hardness and resistance to deformation.
- Aluminum: Lightweight and offers good thermal conductivity, favored for certain applications.
- Alloys: Custom formulations to suit specific production requirements.
The Role of Technological Advancements
The emergence of advanced technologies such as Computer Numerical Control (CNC) machining and 3D printing has revolutionized mold manufacturing processes. These technologies enable manufacturers to produce complex designs with exceptional accuracy, considerably reducing lead times and costs.
Applications of Mold Manufacturing in Metal Fabricators
As a vital component of the metal fabricators industry, mold manufacturers like DeepMould cater to a range of applications:
- Automotive Industry: Producing parts that require durability and functionality.
- Aerospace: Creating high-precision components for aircraft and space vehicles.
- Consumer Electronics: Ensuring tightly integrated components for a seamless fit and function.
Industry-Specific Challenges and Solutions
Different industries come with unique challenges. A skilled mold manufacturer not only navigates these but offers solutions. For instance:
- Complex Geometry: Utilizing advanced simulation software to optimize mold design for intricate shapes.
- Material Limitations: Experimenting with composite materials to enhance strength without adding weight.
- Tight Deadlines: Implementing agile manufacturing practices that allow for rapid prototype development.
Quality Assurance in Mold Manufacturing
At DeepMould, quality is woven into the very fabric of our manufacturing process. A robust quality assurance system encompasses:
- In-Process Inspection: Regular checks during mold fabrication to ensure adherence to specifications.
- Final Product Testing: Rigorous testing of molded products to validate their functionality and durability.
- Client Feedback Integration: Continuous improvement based on client feedback to meet and exceed expectations.
The Importance of Certifications
Certifications such as ISO 9001 are critical for mold manufacturers. They demonstrate a commitment to quality and industry best practices, providing clients with confidence in their manufacturing partners.
Future Trends in Mold Manufacturing
The manufacturing landscape continues to evolve, with trends shaping the future of how molds are created and utilized:
- Sustainability: A growing focus on eco-friendly materials and processes to minimize environmental impact.
- Digital Transformation: The adoption of Industry 4.0 principles, integrating AI and IoT into manufacturing processes.
- Customization: Increasing demand for tailored solutions necessitating flexible mold designs and manufacturing processes.
Conclusion: Why Choose a Leading Mold Manufacturer
In conclusion, choosing the right mold manufacturer is paramount for businesses in the metal fabricators sector. At DeepMould.net, we are committed to delivering state-of-the-art mold manufacturing solutions that not only meet the rigorous demands of our clients but also drive innovation and efficiency in their production processes. With our focus on precision, quality, and customer satisfaction, we are poised to be your partner in successful manufacturing.
Explore our services today, and discover how we can transform your manufacturing capabilities.