Connecting Rod Manufacture: A Comprehensive Guide to Diesel Engine Parts
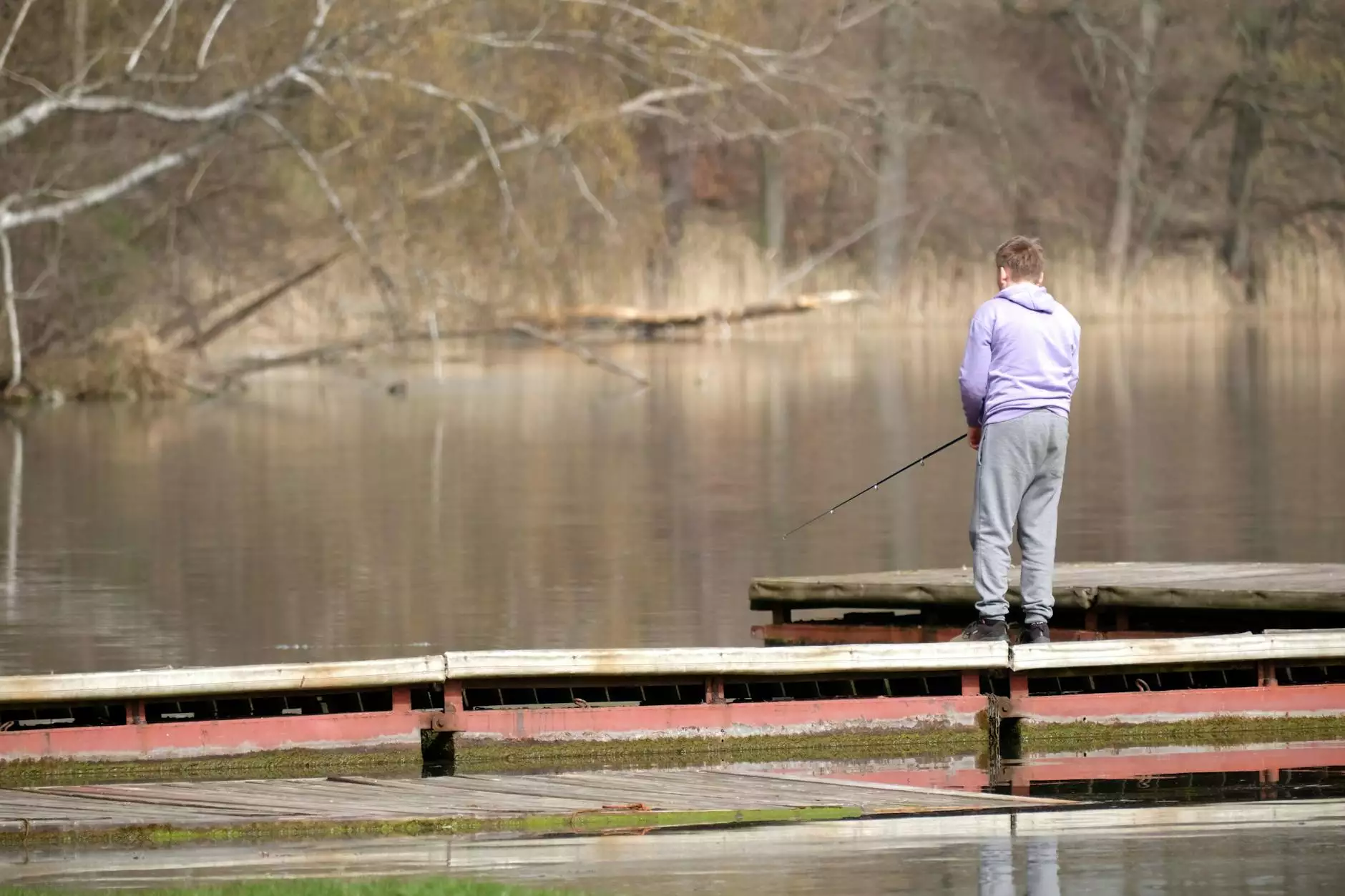
Understanding the Importance of Connecting Rods in Diesel Engines
The connecting rod plays a crucial role in the operation of diesel engines. It serves as the linkage between the piston and the crankshaft. A quality connecting rod not only ensures smooth engine operation but also contributes to overall engine durability. In the diesel engine industry, the demand for high-performance connecting rods is paramount.
What is a Connecting Rod?
A connecting rod is a vital component of the internal combustion engine. It connects the piston, which converts chemical energy from fuel into mechanical energy, to the crankshaft, which converts that energy into rotational motion. The efficiency of this connection can directly affect engine performance, fuel efficiency, and emissions.
The Anatomy of a Connecting Rod
Connecting rods can vary in design and materials, but they generally consist of the following parts:
- Big End: This end connects to the crankshaft, often featuring a bearing to reduce wear.
- Small End: This end attaches to the piston, also utilizing a bearing for smooth movement.
- Rod Body: The main structure that connects the two ends, designed to withstand high tensile forces.
How Connecting Rod Manufacture Works
The process of connecting rod manufacture involves several steps to ensure precision and durability. Manufacturers often use advanced technologies and materials to produce connecting rods that meet strict industry standards.
1. Material Selection
Typically, connecting rods are manufactured using:
- Steel: Known for its strength and durability, steel is a common choice.
- Aluminum: Lightweight and often used in high-performance applications.
- Cast Iron: Provides good wear resistance but is heavier than steel and aluminum.
2. Forging Process
To enhance strength and resilience, many manufacturers utilize the forging process. This involves heating the raw material and then shaping it under high pressure. Forged connecting rods are typically stronger and more reliable than those made with casting methods.
3. Precision Machining
After forging, the rods undergo precise machining to ensure the tolerances required for optimal performance. This includes:
- Turning over the rod body to achieve the correct diameter.
- Drilling holes for the big end and small end bearings.
- Final polishing to enhance surface finish and reduce friction.
Quality Control in Connecting Rod Manufacture
Quality assurance is paramount in the connecting rod manufacture process. Manufacturers perform rigorous testing to validate the strength, durability, and dimensional accuracy of each rod. Common quality control measures include:
- Tensile Testing: Measures the strength of the material under pulling forces.
- Ultrasonic Testing: Detects internal flaws in the rods.
- Dimensional Inspections: Ensures that all specifications are met.
Factors Influencing Connecting Rod Performance
Several factors can influence the performance of connecting rods, including:
- Material Quality: Higher-quality materials usually lead to better performance.
- Design: The design of the rod, including its weight and shape, can affect engine dynamics.
- Manufacturing Process: Advanced manufacturing techniques can enhance performance and longevity.
Finding Reliable Spare Parts Suppliers
When it comes to sourcing connecting rods, it is essential to find reliable spare parts suppliers. Here are some tips:
- Research Suppliers: Look for reputable suppliers in the industry, such as those listed on client-diesel.com.
- Check Reviews: Investigate customer reviews and testimonials to gauge reliability.
- Request Samples: Asking for samples can help determine the quality of the parts before bulk purchases.
Benefits of High-Quality Connecting Rods
Investing in high-quality connecting rods offers numerous benefits to diesel engine operators:
- Increased Reliability: High-quality rods are less likely to fail under high-stress conditions.
- Enhanced Performance: They can contribute to improved engine efficiency and power output.
- Longer Lifespan: Durable rods lead to longer service intervals and lower replacement costs over time.
Advancements in Connecting Rod Technologies
The world of connecting rod manufacture has seen significant advancements in recent years, focused on enhancing performance and reducing weight. Some key trends include:
- Lightweight Materials: Innovations in materials science are leading to lighter connecting rods without sacrificing strength.
- 3D Printing: This technology is being explored for rapid prototyping and manufacturing of unique rod designs.
- Improved Coatings: Advanced coatings can reduce friction and wear, enhancing longevity further.
Conclusion: Investing in Quality for Optimal Performance
The connecting rod manufacture plays an indispensable role in the performance and efficiency of diesel engines. By choosing high-quality rods and working with reputable suppliers like those found on client-diesel.com, operators can ensure their engines run smoothly and efficiently. Remember, investing in quality now can save significant costs and headaches in the long run. Always prioritize reliable sources and advanced technologies to keep your diesel engines performing at their best.